Cormorano
Guest
Hello to all the naval, this is my first post. I press that I am a simple modeler and the yards with which I have to deal at most a table of a couple of meters.
I am trying to make in rhinoceros a hull of a generic sailor (type a. vespucci or down there) and I think that more or less as form I should be there.
My problem is this: after modeling the hull with curves absolutely "fair" or fluent correctly, I get a surface of the hull that still seems well made. If, however, I go to slice it to have the sections of the order, the drawn curves seem far away from being in turn "fair". I have obviously displayed the curves with the appropriate scan/curve/active curve chart. Should the sections not be as fluent as the surfaces from which they were cut? Is it my mistake or maybe the result I get is fine and I could ignore the unfair course of the sections?
thanks to all those who could enlighten me.
I put in some pictures that I hope will clarify the problem.
this is the departure hull:
this is the section profile cut by the hull. very little fair. The white curves of the curvature analysis are quite irregular.
This is what I would expect, given the goodness of the hull used. this has been corrected manually, to make understand the difference between the two results. Curve lines are much more flowing.
What do you think?
Bye.
Horny.
I am trying to make in rhinoceros a hull of a generic sailor (type a. vespucci or down there) and I think that more or less as form I should be there.
My problem is this: after modeling the hull with curves absolutely "fair" or fluent correctly, I get a surface of the hull that still seems well made. If, however, I go to slice it to have the sections of the order, the drawn curves seem far away from being in turn "fair". I have obviously displayed the curves with the appropriate scan/curve/active curve chart. Should the sections not be as fluent as the surfaces from which they were cut? Is it my mistake or maybe the result I get is fine and I could ignore the unfair course of the sections?
thanks to all those who could enlighten me.
I put in some pictures that I hope will clarify the problem.
this is the departure hull:
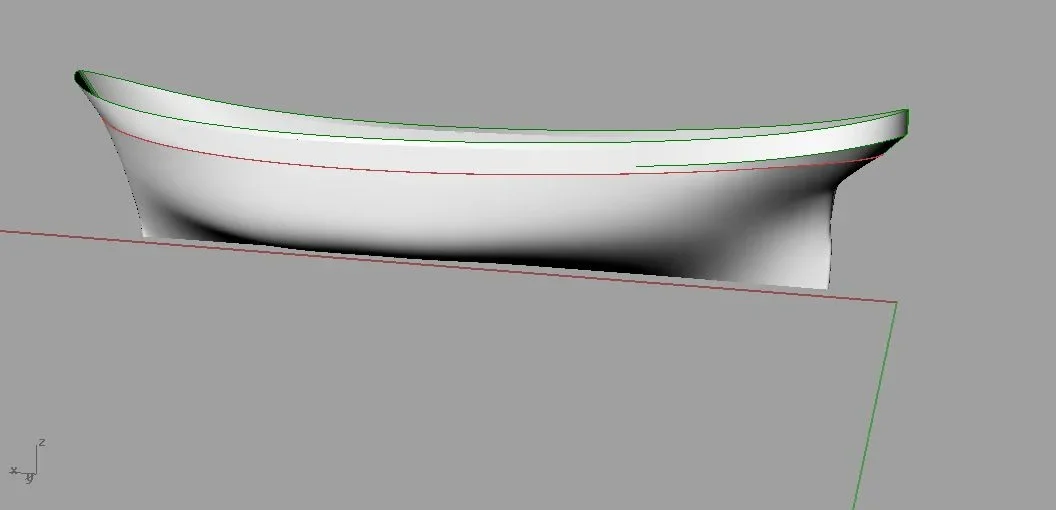
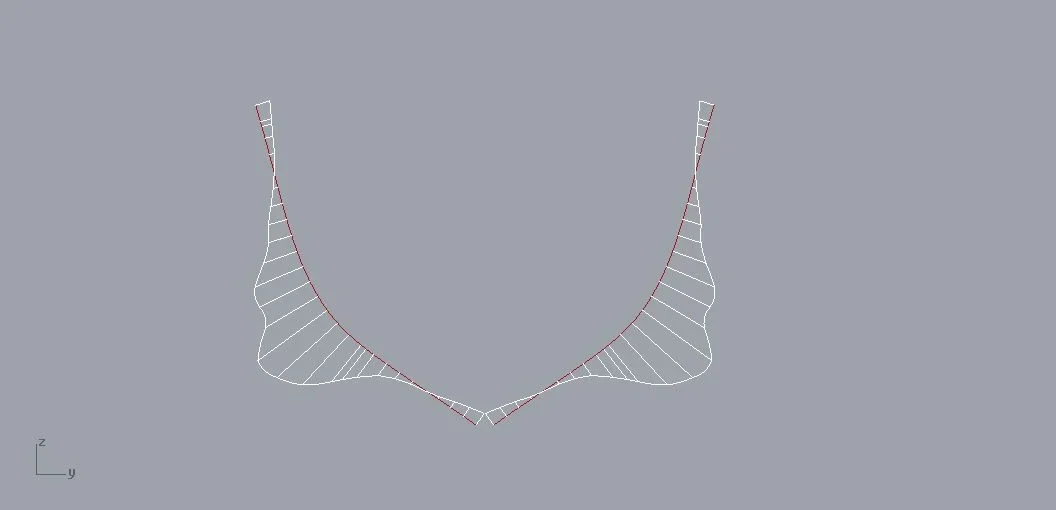
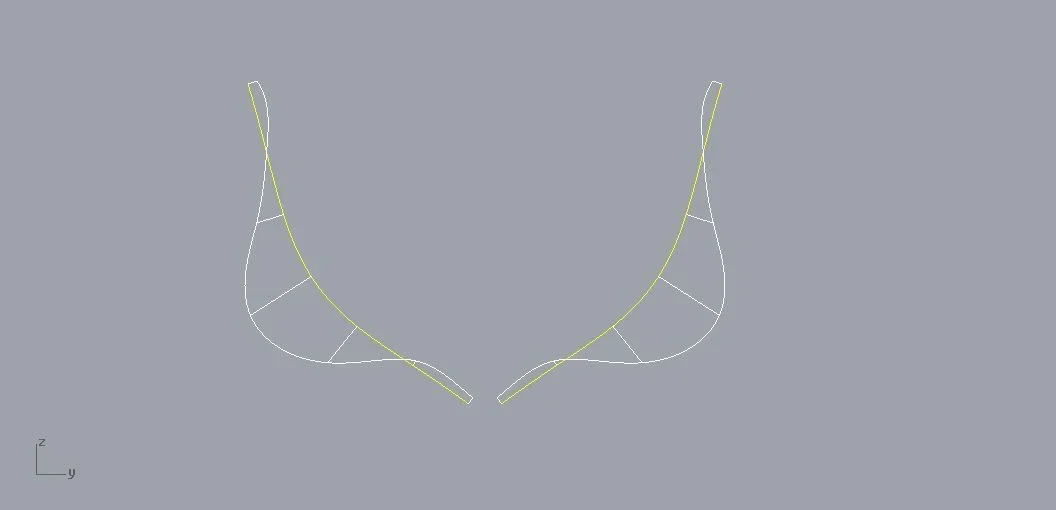
Bye.
Horny.