Calender
Guest
Good morning to all,
we are setting up a test bench for heat exchangers (which cool a product brought at high temperature). the goal is to show the performance of a new exchanger compared to the previous model. It's the first time I've been interfacing with testing equipment and in general hydraulics and heat exchange are not my strong, so I ask advice to the most experienced.
the idea is to use a pump "1" to feed with water the exchangers "6" and "7" (posed at a height of about 2 meters from the ground, for various reasons that I am not discussing while the pump and the tank are on the ground), the valve "2" regulates the flow rate (measured with a flowmeter "3"). before the exchangers a measurement of the temperature and pressure of the water is carried out, measurement that is carried out immediately after (to evaluate heat exchanged and load losses). then the fluid returns to the tank.
there is a replenishment of water in the tank with a system that exploits a float (not present in figure)
Now:
1)valve 4 is for the vent of air, I do not know whether to predict or not other systems to "degas" water, especially when filling. what are the shortcomings you need to keep (there are commercial devices of cost and bulk content you can use in the tank)? I would like to avoid the pump manifesting cavitation phenomena. . .
2) they almost imposed me to use two valves marked in red ("8" and "9") downstream of the heat exchangers, to be closed in the start-up phase to facilitate the pump in the caption. in the past they told me about various types of starters for the pumps, but sincerely I never found detailed indications about it. in my case the pump never works dry. Does anyone pass me some notes or reference where I can study the start of the pumps well? because I have the impression that the fact of putting two valves after the heat exchangers has been proposed without solid theoretical bases (in fact the answer of those who proposed it was always so..).. the methods that I know preview all to act or not on the control valve (according to the type of pump), but of these additional hypothetical valves I have never heard of it. . .
3) to maintain the constant t1, is there any other method besides predicting a possible cooling in the tank itself (with possible chiller)? Would a larger reservoir make it "thermal flow"?
thanks to everyone for the answers
we are setting up a test bench for heat exchangers (which cool a product brought at high temperature). the goal is to show the performance of a new exchanger compared to the previous model. It's the first time I've been interfacing with testing equipment and in general hydraulics and heat exchange are not my strong, so I ask advice to the most experienced.
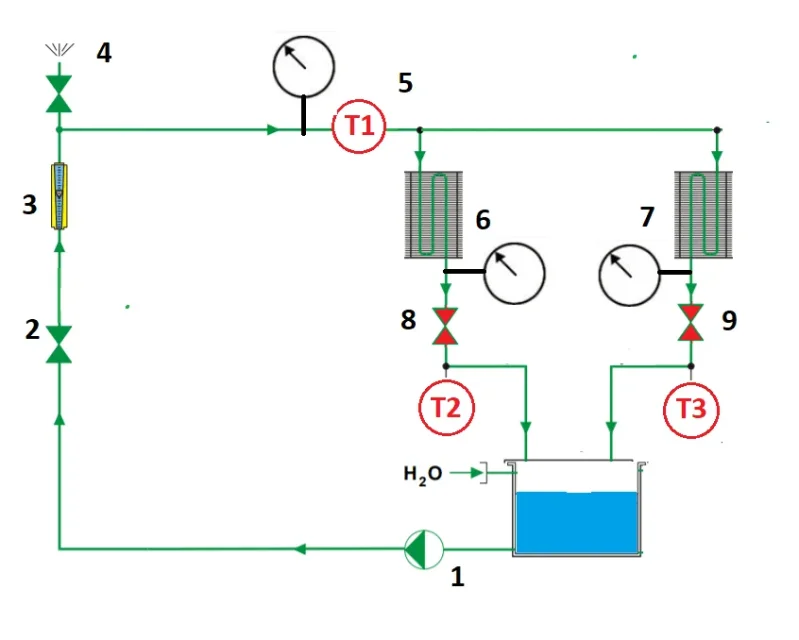
there is a replenishment of water in the tank with a system that exploits a float (not present in figure)
Now:
1)valve 4 is for the vent of air, I do not know whether to predict or not other systems to "degas" water, especially when filling. what are the shortcomings you need to keep (there are commercial devices of cost and bulk content you can use in the tank)? I would like to avoid the pump manifesting cavitation phenomena. . .
2) they almost imposed me to use two valves marked in red ("8" and "9") downstream of the heat exchangers, to be closed in the start-up phase to facilitate the pump in the caption. in the past they told me about various types of starters for the pumps, but sincerely I never found detailed indications about it. in my case the pump never works dry. Does anyone pass me some notes or reference where I can study the start of the pumps well? because I have the impression that the fact of putting two valves after the heat exchangers has been proposed without solid theoretical bases (in fact the answer of those who proposed it was always so..).. the methods that I know preview all to act or not on the control valve (according to the type of pump), but of these additional hypothetical valves I have never heard of it. . .
3) to maintain the constant t1, is there any other method besides predicting a possible cooling in the tank itself (with possible chiller)? Would a larger reservoir make it "thermal flow"?
thanks to everyone for the answers
Last edited: