In the dynamic realm of aircraft design, performance and safety remain paramount. Ground vibration testing (GVT) is an essential step of the aircraft certification process and verification of its aeroelastic stability. However, performing this modal test on a full-scale aircraft under time pressure can be a challenge for testing teams. Siemens recently organized a masterclass to explain all the steps of a ground vibration test campaign and highlight state-of-the-art technologies and best practices to handle this test with confidence and utmost efficiency.
Live demonstrations on full-scale F-16 aircraft: from theory to practical application
The masterclass, attended by over 40 participants representing a diverse array of companies and countries, brought together aviation experts and industry leaders. The aerospace landscape was well-represented, with companies such as Airbus, Lilium, Hellenic Air Force and other commercial and military aircraft companies. The event’s comprehensive agenda covered a spectrum of topics, from theoretical discussions on structural dynamics to live demonstrations of GVT procedures on an actual aircraft.
During the four days, the master class rolled out an integrated approach to handle test preparation, modal testing, modal analysis, numerical model correlation, model updating and model exploitation. The presence of a full-scale F-16 aircraft as the focal point added a tangible and impactful dimension to the masterclass. Practical aspects such as aircraft suspension, instrumentation or shaker excitation using pseudo-random, sine or phase resonance techniques were discussed in detail. State-of-the-art modal curve-fitting algorithms such as Polymax or Maximum Likelihood estimation of a Modal Model (MLMM) were also presented and used to process the frequency response functions (FRF) acquired on the F-16 aircraft.
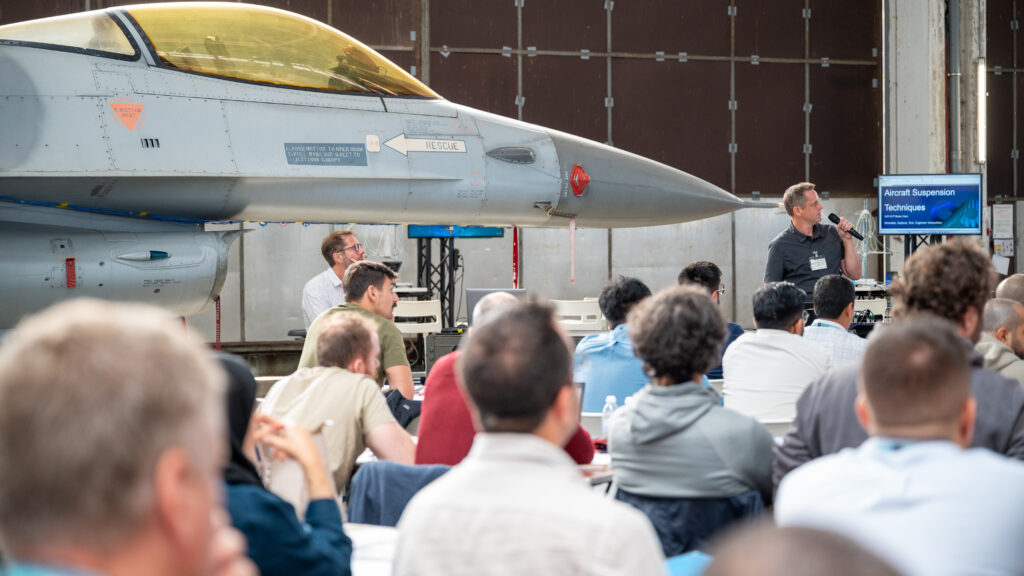
Special moments were numerous, with engaging panel discussions featuring experts from industry and academic who shared insights into the challenges of such critical certification tests and latest advancements within the aerospace testing domain.
Expert guest speakers for the GVT Masterclass Europe 2023 included, next to Siemens experts:
- Wim Doeland, Structures Expert at European Aviation Safety Agency (EASA)
- Julian Sinske, Team Lead Structural Dynamics Testing at DLR, German Aerospace Center
- Jonathan Cooper, Aerostructures and Aeroelasticity Expert and Professor at University of Bristol, UK
- Gaetan Kerschen, Professor of Aerospace Engineering at University of Liège, Belgium
Hands-on activities: learning by doing
There is no better way to learn than by doing the test by yourself. During the hands-on activities planned every day of the masterclass, participants were split into small groups and ran the entire test sequence by themselves. Scaled aircraft models allowed participants to rehearse the different steps of the test from instrumentation check to actual data collection and analysis with various excitation signal types.
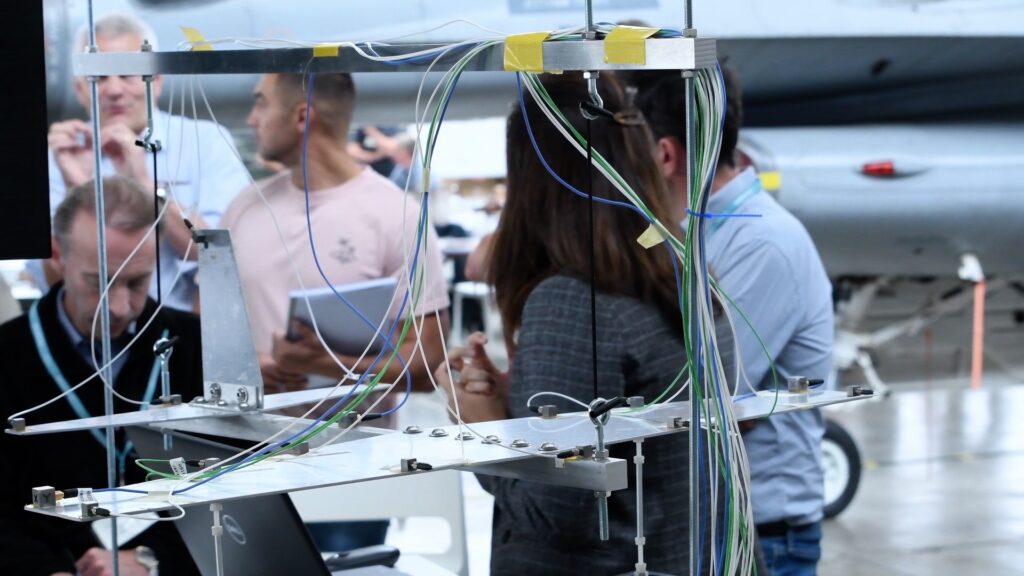
Unique learning and networking opportunity
One of the invaluable aspects of the masterclass was the opportunity for attendees to network with like-minded individuals. Whether during breakout sessions, lunches or informal networking sessions, participants had many opportunities to exchange ideas and forge new connections.
Aside from meeting their peers from various countries and different aircraft companies, participants also exchanged with experts from Siemens and guest speakers from the industry and the academic world. Attendance of representatives from PRODERA, PCB Piezotronics, Sandow Technic and Fabreeka also allowed participants to learn about latest sensors, modal shakers, and aircraft suspension technologies.
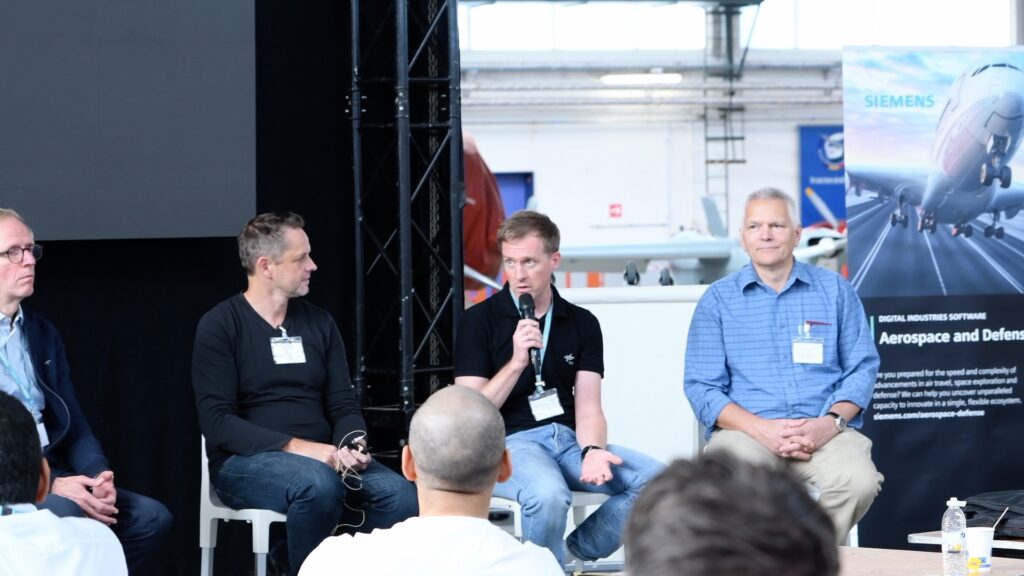
Feedback from attendees echoed a resounding appreciation for the depth and breadth of knowledge shared by the Siemens experts and the guest speakers. Participants found the masterclass not only informative but also instrumental in expanding their understanding of ground vibration testing. Learning how to avoid common mistakes in such large-scale modal test, getting insights into latest excitation and processing techniques and understanding how the collected data fits in the connected verification and certification digital thread were some of the key take-aways of the class. Many highlighted the perfect balance between theoretical presentations and live demonstrations on the full-scale aircraft followed by practical hands-on sessions. One participant noted:
The live demonstrations were a game-changer. It’s one thing to read about these processes, but to witness them in action on a full-scale aircraft was truly eye-opening.
Handling next GVT campaigns with confidence
By providing resonant frequencies, mode shapes, damping and scaling factors on the actual aircraft before the first flight, ground vibration testing is an essential step in the aircraft verification and certification process. Making sure that data is measured accurately and in a timely manner can be quite challenging for the engineering teams involved. This four-day GVT masterclass allowed to highlight the state-of-the-art techniques available to handle this test with confidence, going through the entire process from measurement preparation to data acquisition, processing, and reporting.
As the masterclass event ended, the air was filled with a sense of accomplishment and inspiration. Participants left equipped with new skills, fresh perspectives, and new contacts within their industry, feeling empowered for next GVT campaigns.
Siemens remains committed to pushing the boundaries of what’s possible in aircraft testing. This event is also an occasion for our research teams to experiment innovative techniques on a full-scale instrumented aircraft. Video motion magnification is an example of such techniques that can bring valuable insights in modal testing of large structures. By using a high-resolution camera while the structure is being excited, tiny vibrations are amplified and deformation of the structure for a specific mode shape becomes clearly visible.