“When I was young, there were no signs of an electric drive or electrified vehicles. Car adverts were about speed and horsepower. Now, they are all about range and zero emissions,” comments Steven Dom, Director, Automotive Industry Solutions at Siemens Digital Industries Software.
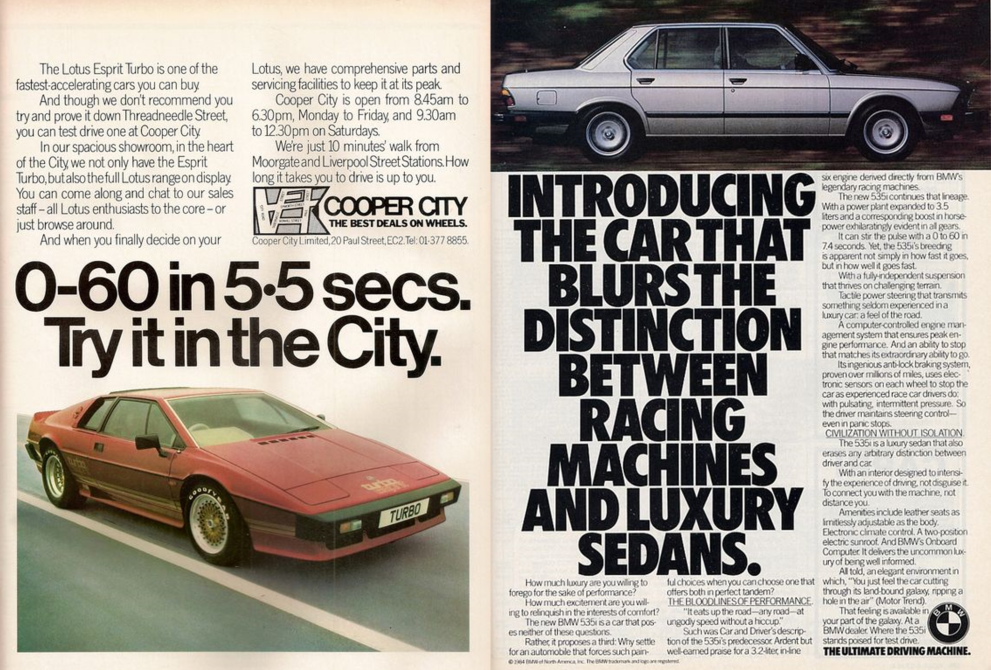
As electric vehicles (EVs) have changed advertising, they have also changed engineering. “A team of engineers tasked with developing a combustion engine might choose to buy or design a gearbox,” continues Steven. “As long as they meet the vehicle specification, the decision is theirs. That type of solo decision-making is not possible in EVs, where the trend is clearly to go to integrated electric drive units or e-drives in which the power electronics, motor, and transmission system which make up the drive are packaged as one entity. From a manufacturing perspective, it is easier to build one integrated box, but to get that package right, there must be an ongoing conversation between each distinct engineering discipline. For some individuals and organizations, this will be an enormous challenge.”
Managing the challenges of electric drive systems engineering
Siemens experts Steven Dom and Benoit Magneville, Electrification Product Manager, addressed all aspects of electric-drive systems development and how organizations can support engineering teams and embrace closer collaboration.
As Benoit explains: “The overall aim is to design an electric drive that is highly efficient in a wide range of operating conditions, yet there are many potentially conflicting requirements. Reducing the distance between the inverter and the motor, for example, presents benefits in terms of overall package size, cable weight, and harnessing; however, it creates new thermal and mechanical challenges as the inverter is evolving more restrained way.”
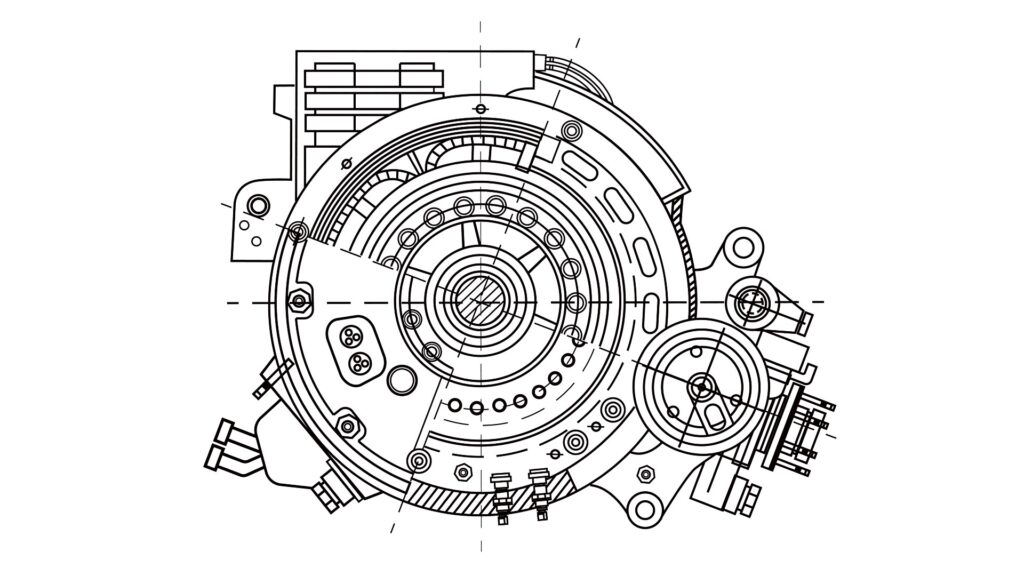
Other challenges related to thermal cooling include a critical requirement within a package of heat-producing items. Considering separate cooling systems for each component in an e-drive is not the most efficient approach. Integrating the cooling system for all components will simplify construction, doing away with an array of pipes, pumps, and heat exchangers. Still, it also makes for a more complex engineering task. On top of this, the battery and the passengers compete for effective thermal management, and appropriate cooling will need to be provided.
In addition, there is a complex dynamic between meeting operational targets for the e-drive and predicting how noise and vibration are perceived by people sitting in the cabin. From a commercial perspective, passenger comfort is essential to manufacturers, particularly for high-value brands.
Addressing Power Electronics design, system integration, and reliability
Topology design is one of the early stages of developing an electric drive’s electronics. Key metrics must be understood to define the best topology, such as efficiency, cost, tolerance, and EMI suppression. Much engineering time can be spent assessing how topology impacts the vehicle, then optimizing based on those results. However, the effort can be wasted if thermal implications are only discovered at the end of that process. Ideally, thermal design and simulation are entirely in sync with topology design and evaluation.
The choice of semi-conductor technology is also important. Still, the best decisions cannot be made if you do not know how to identify a semiconductor’s characteristics and compare available options. “The ability to understand junction temperature is key because that defines reliability,” says Benoit. “You cannot just rely on performance ratings from a supplier or on one set of test results.”
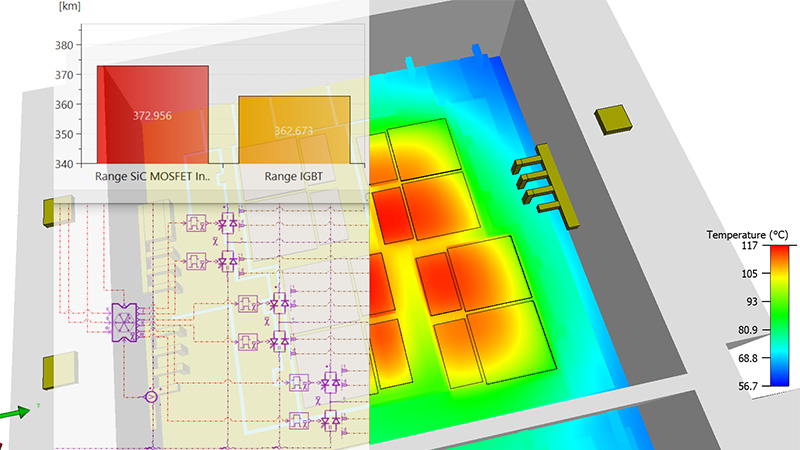
A thorough and accurate electronics design exploration encompassing PCB (Printed Circuit Board) and Busbar design requires integration with mechanical CAD and electromagnetic, thermal, and structural analysis. The solution is for development to take place within a single environment in which all engineers have easy access to other disciplinary areas, and specialists can interact with each other.
The ATZ International webinar will explain how to build a Simcenter workflow that incorporates design, simulation, and testing optimizes power electronics devices, and delivers the required power density in a reliable, compact package that ensures EMI/EMC compliance and performance.
From early electric motor sizing up to performance validation
One fundamental requirement is that a motor’s lifetime is reliably higher than the vehicle warranty and the vehicle’s lifetime. Thermal design is one of the main ways to improve lifetime and performance.
“As usual, success begins with the design phase,” notes Benoit. “Electric motor requirements are cascaded down from EV performance targets. The best way to obtain fast and accurate motor sizing and configuration is to quickly evaluate multiple design types and topologies against electro-magnetic efficiency, thermal and thermal and vibro-acoustics performance while still in the architectural phase.”