Whether we’re talking about the latest electric vehicle, a hybrid, or a traditional gasoline car, they all share a critical need: keeping temperatures “just right.” Vehicle energy and thermal management is like conducting an orchestra where every instrument needs to play at the perfect volume. When it works, it’s beautiful. When it doesn’t… well, that’s when you notice.
The EV revolution has turned up the heat on this challenge. Every watt of power used for cooling or heating directly impacts how far you can drive on a charge. The lessons we’re learning from EVs are helping make all vehicles more efficient, regardless of what’s under the hood.
Optimizing vehicle energy and thermal management
Traditional siloed engineering approaches just don’t cut it anymore. Developing the cooling system separately from the powertrain, which is separate from the cabin comfort system? That’s like trying to build a house by having different contractors work without talking to each other. It might stand up, but it won’t be very efficient!
An integrated approach is required to bring everything together from day one. This is where advanced simulation and testing tools come into play, allowing engineers to see the big picture before the first prototype is even built.

Simcenter’s integrated VEM-VTM solutions cover all development stages from requirements, benchmarking, architecture and sizing, to VTM components engineering and vehicle integration.
Let’s dive deeper into how this modern approach is revolutionizing vehicle development…
1 – VEM benchmarking and target setting
At the dedicated VEM facility, existing vehicles are fitted with sensors to identify all the mechanical, electrical, and thermal energies flowing through them. Different scenarios are run, such as normal driving, cold start, hot start, and charging, to capture the complete behavior of the vehicle in various conditions. Engineers use this data to create a digital twin that can be modified to explore potential improvements and optimization. Any aspect of the car can be changed, such as the size or type of battery, the HVAC system, or the positioning of different components, and then run simulations to see how this affects overall performance.
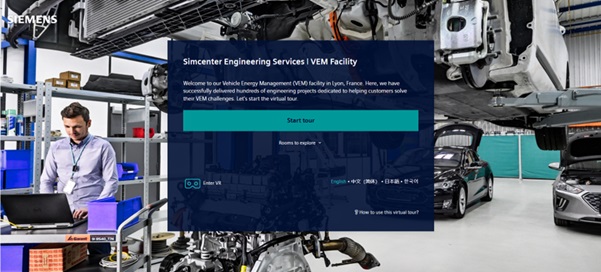
Want to know more about VEM benchmarking?
2 – Vehicle architecture definition
Vehicle architecture definition focuses on establishing system requirements and initial sizing to meet performance targets. Key activities include selecting the powertrain type, defining thermal system architecture, sizing key components such as the motor and the battery, and determining cooling/heating needs.
OEMs utilize supplier data and models to validate initial sizing and develop thermal strategies. This enables early identification of integration challenges and allows for architecture optimization. The process supports efficient development of thermal management systems while balancing performance and comfort requirements.
This data-driven approach helps OEMs integrate thermal considerations from the start, enabling faster development of energy-efficient vehicles.
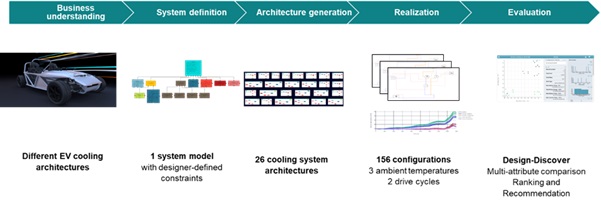
For more information on the vehicle architecture, read the article in Charged EV on how to use generative engineering in EV architecture exploration.
3 – Sizing and system development
VEM sizing is like creating a balanced energy blueprint for a car. How much energy storage do we need for the desired driving range? How strong must the electric motor be for acceleration, hill climbing, highway speeds? How will the power electronics manage the power flow between the battery and motor? Will the cooling system keep everything at safe operating temperatures?
All building blocks need to fit perfectly together. If one component is too small or too large, it affects the entire system’s performance. The goal is to find the sweet spot where everything works together efficiently while meeting all requirements.
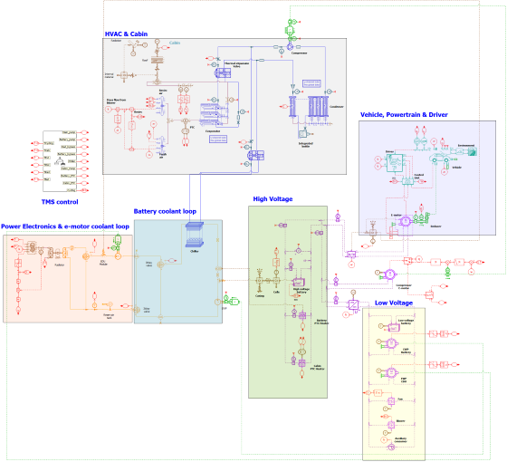
4 – Detailed components engineering
Over their lifetime, vehicle components are repeatedly exposed to temperatures up to several hundred degrees Celsius. Without adequate thermal management, this will lead to component failure, causing significant safety and cost issues.
Simcenter solutions help designers predict the thermal behavior of each component to understand the required cooling levels. They also help ensure that batteries in electric vehicles remain within the optimum operating temperature to deliver maximum performance and guarantee safety.
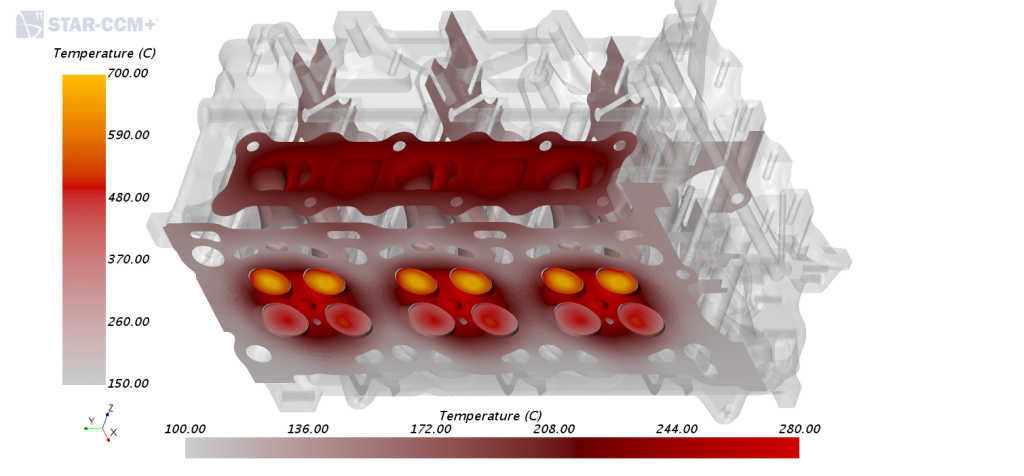
The integrated simulation also allows engineers to optimize cabin thermal comfort alongside vehicle performance. Comfort is becoming an increasingly important differentiator, especially in luxury vehicles, so comfort must be optimized without impacting performance.
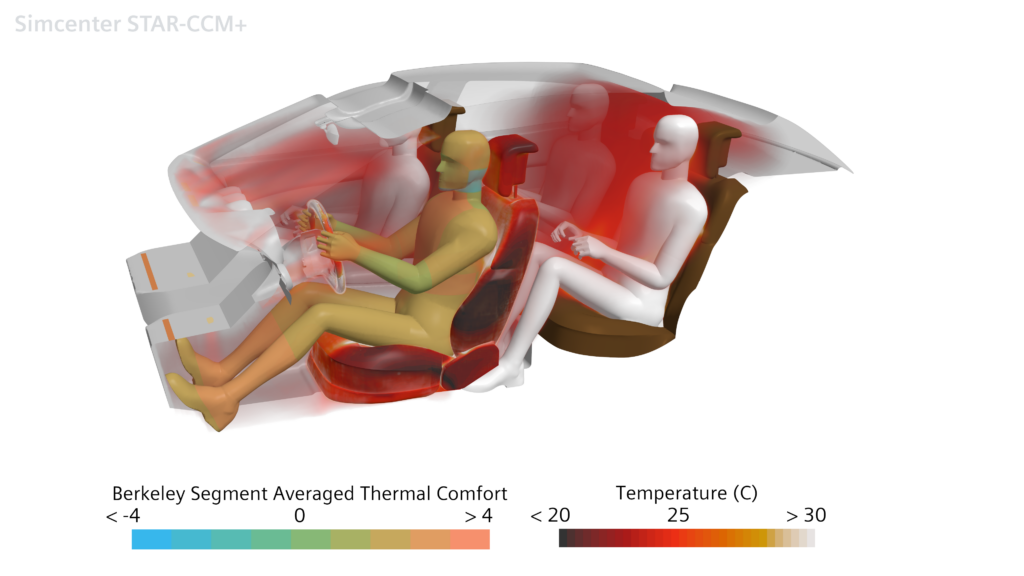
Read the following resources for more info on component thermal management:
- Blog on battery modeling and safety, from the 3D cell design right through to the full battery pack and thermal propagation during a runaway event.
- Recordings of the latest ICE thermal workshop where industry experts shared the latest simulation developments for internal combustion engines
- Watch the cabin thermal comfort webinar to discover how high-fidelity simulation helps to design efficient HVAC control systems or read how Calsonic Kansei Corporation, now merged with Magneti Marelli and now known as Marelli, reduced the number of physical prototypes by half for designing air conditioning systems.
5 – Full vehicle integration
For modern vehicles, a holistic view is essential from the outset, as countless interdependent factors influence energy usage and thermal management. Failing to integrate these elements early leads to costly, time-consuming design changes later.
Virtual integration is through system-level simulation is a key enabler, allowing cross-functional teams to break down traditional silos and collaborate effectively. A digital thread connects the evolving subsystems, ensuring the latest models are integrated throughout development. This empowers each discipline to understand how their work impacts – and is impacted by – the broader vehicle system.