Cast16
Guest
Bye to all,
as from title, how to calculate the max stress and deflection of the folded sheet section (s275 thickness 5mm section 45-60-45mm) with 200 kg weight as in the attached photo. everything will eventually be tested and certified by an external consultant, but I am trying to test it with fea of inventor in the design phase. are in the first weapons with fea, and the completely different results between stress analysis and nastran are not helping. I wanted to see what the results of manual calculations would be.
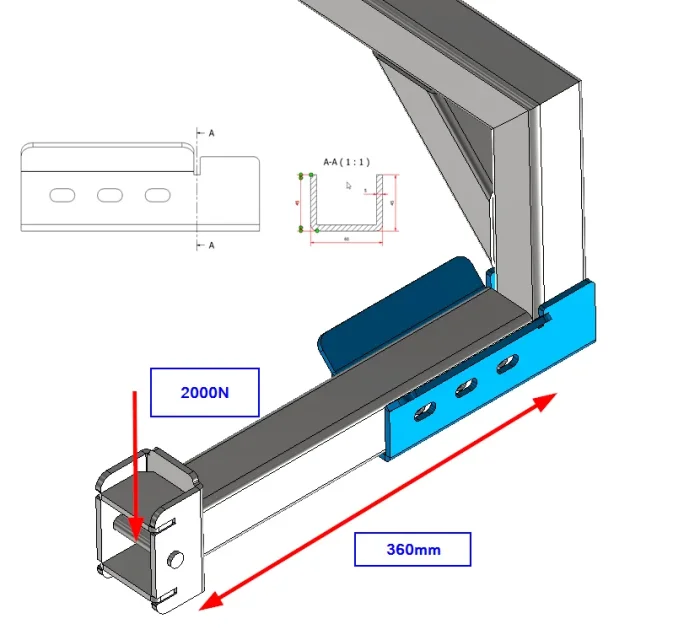
as from title, how to calculate the max stress and deflection of the folded sheet section (s275 thickness 5mm section 45-60-45mm) with 200 kg weight as in the attached photo. everything will eventually be tested and certified by an external consultant, but I am trying to test it with fea of inventor in the design phase. are in the first weapons with fea, and the completely different results between stress analysis and nastran are not helping. I wanted to see what the results of manual calculations would be.
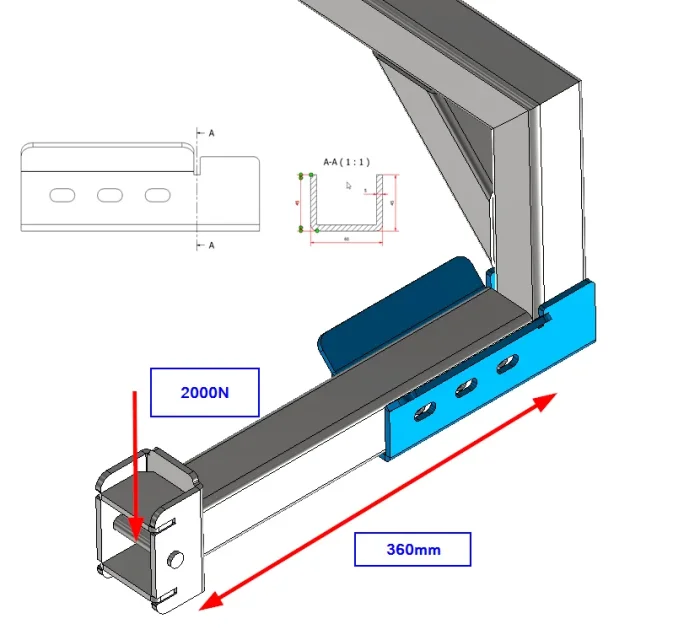