meek851
Guest
Good evening to all,
I came across this image (taken from the schaffler site).
I noticed that the shaft is supported by 3 bearings (two conical rollers and one roller). They always told me that 3 or more bearings should never be mounted on a tree (because it is difficult if not impossible to align them). the system would be hyperstatic and difficult to calculate, force could arise. However there are those who argue that putting another bearing as in image increases system life (absorbing a radial load) and would like to improve our machines so. What do you think?
Do you ever use more than two bearings?
What are the shortcomings to take? What are the advantages/disadvantages?
Thank you.
I came across this image (taken from the schaffler site).
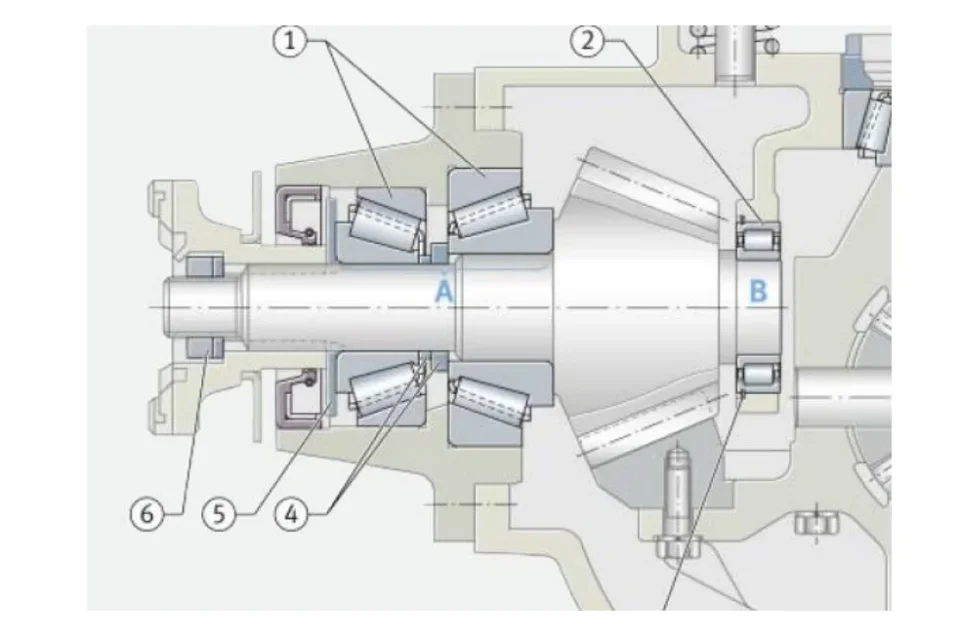
Do you ever use more than two bearings?
What are the shortcomings to take? What are the advantages/disadvantages?
Thank you.