meccanicamg
Guest
Nous abordons le problème de la vérification des soudures selon les normes actuelles. nous devons utiliser en iso 1993-1-8 pour l'analyse de fatigue nous devons utiliser en iso 1993-1-9.
Bien, alors nous apportons un exemple très simple: un joint en t avec cordons latéraux avec une force de traction appliquée de 500kn.
matériau de cordon d'articulation et d'angle s355jr ex fe510.
de ce schéma nous avons deux façons de calculer statiquement notre soudage:
- méthode simplifiée: en utilisant la valeur de résistance du cordon et en comparaison avec la demande de résistance de l'objet, nous avons un facteur de sécurité supplémentaire fsa = 0,05- méthode directionnelle : en utilisant des tensions générées dans la section gorge (non renversée), vous obtenez un facteur de sécurité supplémentaire fsa = 1,8- juste que nous vérifions également selon ntc 2018 et nous voyons un facteur de sécurité supplémentaire fsa = 1,4.
déjà ici, nous nous demandons si les deux méthodes sont réellement fiables. probablement la méthode simplifiée, en tant que telle est très prudent contrairement à la méthode directionnelle qui est complète et plus réaliste. la méthode nationale, fournit une valeur intermédiaire pour les deux conformément. Le fait est que notre joint soudé ne se brise pas.
maintenant nous passons la fatigue de la parole et donc ici nous devons prendre en iso 1993-1-9 et les indications iiw (qui est l'institut international de (w)sauvetage) et déjà ici nous nous rendons compte que la norme se réfère à quelque chose de très ouvert et douteux.
Nous commençons à garder à l'esprit que l'épaisseur de la feuille est supérieure à 25 mm, donc nous devons garder à l'esprit l'épaisseur du coefficient de corrélation que dans notre cas ks=0,8. Compte tenu des paramètres fixes pour les calculs où le coefficient d'évaluation des dommages prend 1,25 et la multiplication de tension égale à 1 et nous faisons que nous appliquons une charge minimale de 0kn jusqu'à notre 500kn et nous répétons cycliquement le spectre de charge.
selon la méthode normale rapportée dans la norme, après avoir pris la catégorie correspondante de jonction, vous pourriez arriver à 5.1e+04 cycles d'obtenir un dommage de 99,17 %. Eh bien, alors on dit: parfait tous ces cycles sont bons pour moi et je fais l'application pour 1000 cycles moins et sont appropriés.
alors, pas heureux nous allons de l'avant dans la norme et découvrir qu'il y a une méthode appelée stress des points chauds où il est nécessaire de réaliser ou une pièce physique pour tester ou un modèle solide avec des éléments finis et vérifier ce qui se passe.
d'abord, nous modélisons le joint de façon réelle, c'est-à-dire en partant 2 mm d'air entre les deux plaques afin que ce soit seulement le cordon de soudage pour réagir aux efforts (ce qui n'est pas possible si les deux plaques ont été combinées contact global).
Nous choisissons d'utiliser la méthode de l'extrapolation carrée non liée à l'épaisseur, donc nous décidons de réaliser, selon l'indication du iiw une maille qui a la marche moins ou égale à 4 mm... bien loin avec la maille solide 4 mm.
la méthode prévoit le retrait de la tension principale ps1 qui est l'effet de la traction pure à 4, 8 et 12 mm sur la plaque à l'examen, à partir du pied du soudage au cordon.
par cette méthode il s'avère que pour obtenir un dommage de 99 % je ne peux atteindre 9.5e+03 cycles. Cette valeur est bien inférieure à la précédente et est la valeur limite de l'application. Cependant, la norme ne dit pas qu'il est nécessaire d'utiliser toutes les méthodes de vérification et de choisir la plus conservatrice.
C'est pourquoi la première méthode d'essai de fatigue est également tenue d'utiliser la deuxième valeur et d'obtenir ainsi un facteur de sécurité supplémentaire. fsa=5 alors qu'avec la deuxième méthode je me retrouve avec fsa=1.
Donc la domandone est: avec cette règle, comment la vérification statique+fatigue a-t-elle vraiment lieu? Quelles informations réelles avez-vous sur la vérification avec la méthode des points chauds?autre chose que je n'ai pas compris est le discours de la reconstitution de la distension. Selon la norme, 60% de la valeur de la tension minimale peut être ajoutée à la tension de traction réelle. belle... a péché qu'un cycle de charge à partir de zéro... Ses 60% valent zéro. Je ne pense pas qu'une structure relogée et non réglementée soit égale à 0kn à 500kn.
Avez-vous des directives ?
Bien, alors nous apportons un exemple très simple: un joint en t avec cordons latéraux avec une force de traction appliquée de 500kn.
matériau de cordon d'articulation et d'angle s355jr ex fe510.
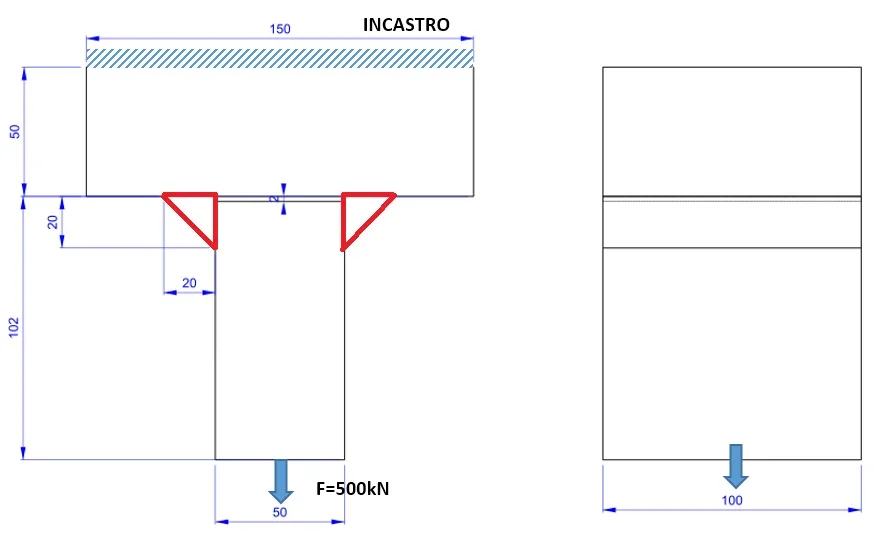
- méthode simplifiée: en utilisant la valeur de résistance du cordon et en comparaison avec la demande de résistance de l'objet, nous avons un facteur de sécurité supplémentaire fsa = 0,05- méthode directionnelle : en utilisant des tensions générées dans la section gorge (non renversée), vous obtenez un facteur de sécurité supplémentaire fsa = 1,8- juste que nous vérifions également selon ntc 2018 et nous voyons un facteur de sécurité supplémentaire fsa = 1,4.
déjà ici, nous nous demandons si les deux méthodes sont réellement fiables. probablement la méthode simplifiée, en tant que telle est très prudent contrairement à la méthode directionnelle qui est complète et plus réaliste. la méthode nationale, fournit une valeur intermédiaire pour les deux conformément. Le fait est que notre joint soudé ne se brise pas.
maintenant nous passons la fatigue de la parole et donc ici nous devons prendre en iso 1993-1-9 et les indications iiw (qui est l'institut international de (w)sauvetage) et déjà ici nous nous rendons compte que la norme se réfère à quelque chose de très ouvert et douteux.
Nous commençons à garder à l'esprit que l'épaisseur de la feuille est supérieure à 25 mm, donc nous devons garder à l'esprit l'épaisseur du coefficient de corrélation que dans notre cas ks=0,8. Compte tenu des paramètres fixes pour les calculs où le coefficient d'évaluation des dommages prend 1,25 et la multiplication de tension égale à 1 et nous faisons que nous appliquons une charge minimale de 0kn jusqu'à notre 500kn et nous répétons cycliquement le spectre de charge.
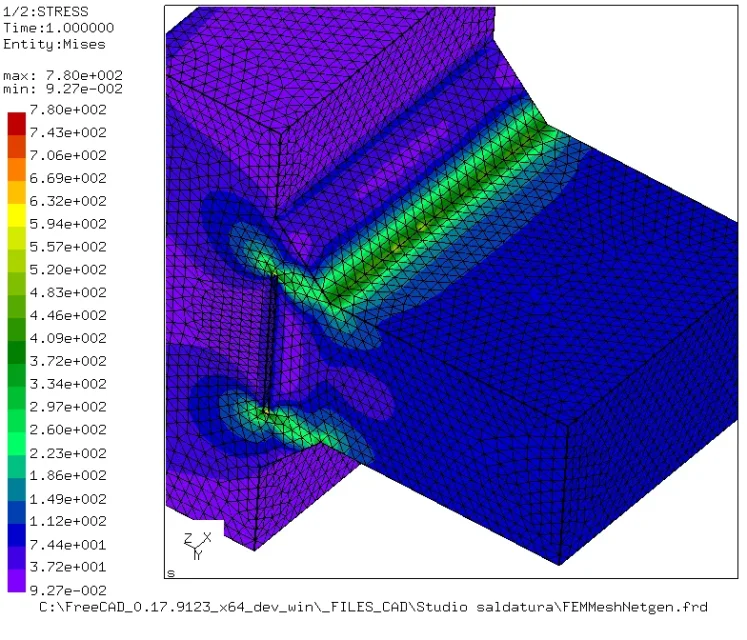
alors, pas heureux nous allons de l'avant dans la norme et découvrir qu'il y a une méthode appelée stress des points chauds où il est nécessaire de réaliser ou une pièce physique pour tester ou un modèle solide avec des éléments finis et vérifier ce qui se passe.
d'abord, nous modélisons le joint de façon réelle, c'est-à-dire en partant 2 mm d'air entre les deux plaques afin que ce soit seulement le cordon de soudage pour réagir aux efforts (ce qui n'est pas possible si les deux plaques ont été combinées contact global).
Nous choisissons d'utiliser la méthode de l'extrapolation carrée non liée à l'épaisseur, donc nous décidons de réaliser, selon l'indication du iiw une maille qui a la marche moins ou égale à 4 mm... bien loin avec la maille solide 4 mm.
la méthode prévoit le retrait de la tension principale ps1 qui est l'effet de la traction pure à 4, 8 et 12 mm sur la plaque à l'examen, à partir du pied du soudage au cordon.
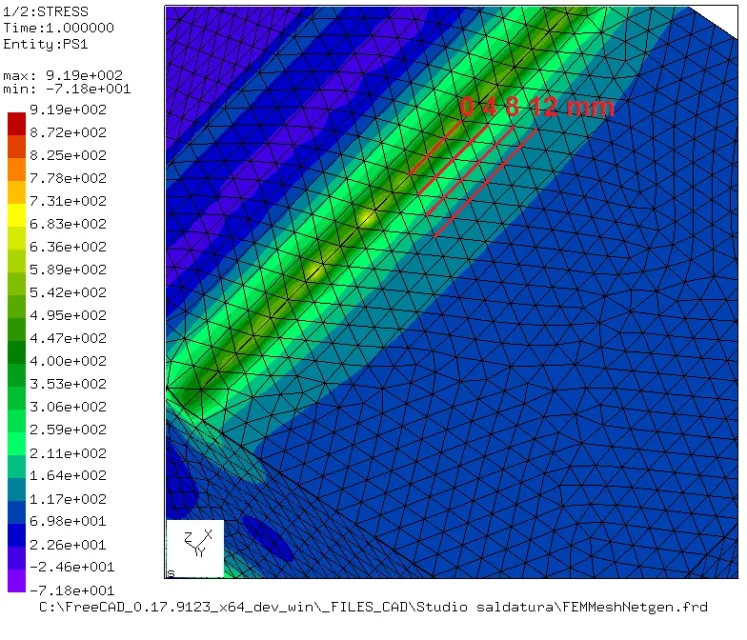
C'est pourquoi la première méthode d'essai de fatigue est également tenue d'utiliser la deuxième valeur et d'obtenir ainsi un facteur de sécurité supplémentaire. fsa=5 alors qu'avec la deuxième méthode je me retrouve avec fsa=1.
Donc la domandone est: avec cette règle, comment la vérification statique+fatigue a-t-elle vraiment lieu? Quelles informations réelles avez-vous sur la vérification avec la méthode des points chauds?autre chose que je n'ai pas compris est le discours de la reconstitution de la distension. Selon la norme, 60% de la valeur de la tension minimale peut être ajoutée à la tension de traction réelle. belle... a péché qu'un cycle de charge à partir de zéro... Ses 60% valent zéro. Je ne pense pas qu'une structure relogée et non réglementée soit égale à 0kn à 500kn.
Avez-vous des directives ?